SCARA Robot THL 500, 600 and 700
Shibaura Machine SCARA robot series
Light models THL 500, 600 and 700.
- Overview -
Light-weight
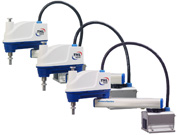
Up to 50% lighter than our previous models!
Capable of reducing environmental impact.
Energy-efficient
Up to 50% reduction in required power supply capacity compared
with our previous models!
Low-power consumption robots ideal for energy conservation era.
- Specifications -
Model | THL500 | THL600 | THL700 | |
---|---|---|---|---|
Arm length (1st Arm + 2nd Arm) | 500 mm (200 mm + 300 mm) |
600 mm (300 mm + 300 mm) |
700 mm (400 mm + 300 mm) |
|
Working envelope | Axis 1 | ±125 deg | ±125 deg | ±125 deg |
Axis 2 | ±145 deg | ±145 deg | ±145 deg | |
Axis 3(Axis Z) | 0~150 mm | 0~150 mm | 0~150 mm | |
Axis 4(Axis C) | ±360 deg | ±360 deg | ±360 deg | |
Maximum speed | Axis 1 | 450 deg/s | 450 deg/s | 450 deg/s |
Axis 2 | 450 deg/s | 450 deg/s | 450 deg/s | |
Axis Z(Axis 3) | 2,000 mm/s | 2,000 mm/s | 2,000 mm/s | |
Axis C(Axis 4) | 1,700 deg/s | 1,700 deg/s | 1,700 deg/s | |
Composite (Axis 1 and 2 composite) |
6,300 mm/s | 7,100 mm/s | 7,900 mm/s | |
Standard cycle time (with 2 kg load) *1 | 0.45 s | 0.45 s | 0.50 s | |
Maximum payload mass *2 | 10 kg (rated:2 kg) |
10 kg (rated:2 kg) |
10 kg (rated:2 kg) |
|
Allowable moment of inertia *2 | 0.2 kg·m2 | 0.2 kg·m2 | 0.2 kg·m2 | |
Positioning repeatability *3 | X-Y | ±0.01 mm | ±0.01 mm | ±0.01 mm |
Axis Z(Axis 3) | ±0.015 mm | ±0.015 mm | ±0.015 mm | |
Axis C(Axis 4) | ±0.007 deg | ±0.007 deg | ±0.007 deg | |
Hand wiring | 8 inputs and 8 outputs | 8 inputs and 8 outputs | 8 inputs and 8 outputs | |
Hand pneumatic joint | Φ6×3pcs | Φ6×3pcs | Φ6×3pcs | |
Robot controller cable | 3.5 m | 3.5 m | 3.5 m | |
Power supply | 1.4 kVA | 1.4 kVA | 1.4 kVA | |
Mass | 22 kg | 23 kg | 24 kg | |
Connectable controller |
|
|
|
|
CAD Files |
|
|
|
*1: Continuous operation is not possible beyond the effective load ratio.
・Horizontal 300 mm, vertical 25 mm, round-trip with coarse positioning.
*2: Acceleration/deceleration rates and maximum speed may be limited according to the motion pattern, load mass and amount of offset.
*3: Positioning repeatable accuracy in one-direction movement, when the environmental temperature and robot temperature are constant. It is not the absolute positioning accuracy.
・The specification value may be exceeded depending on moving pattern, load mass and offset amount.
・Positioning repeatability for X-Y and C are for when Z-axis is at the uppermost position.
*4:Pneumatic joints for hand are provided on the base. Pipes are to be provided by the customers.
* Trajectory accuracy is not ensured.