High Precision Machining Center UVM Series
Features
UVM Series has been developed with the concept of high speed and high quality machining, providing High Precision Aerostatic Bearing Spindle. This is a high precision machine and one of application targets is a precision mold.
This machine helps ensuring reduction in the running costs and a significant improvement of the machining quality when compared with the conventional machines.
The following specific effects can be expected:
- 60,000 min-1 spindle installed as standard
=> Reduction in the machining time - Virtually unlimited life of the spindle by using non-contact air bearings
If the spindle is damaged by any chance, the repair costs are much less than the spindles of other machines.
=> Reduction in the maintenance costs - Enhancing tool life by achieving high rotational accuracy of the spindle
In addition, there is no restriction on time for running the spindle at high speed, and machining can be performed with only small-diameter tools. - Significant improvement of machined surface quality
=> Reduction in man-hours for polishing - Significant improvement of machining accuracy
=> Realization of high-valued added machining - Realization of various machining operations by only the machine with a variety of optional accessories such as a rotary table
=> Realization of various types of functions with the machine itself -
Various functions to support high precision and automation
・ Total support application software “UVM-TSA”
Versatile house made software to support high precision machining and automation・ Imaging type tool contour measuring system “FormEye®”
Tool measurement device that accurately measure cutter contour shapes during high-speed rotation・ Imaging type workpiece measuring system “ShapeEye”
On-machine camera measurement device that demonstrate power for high-precision tailoring of fine shapes that cannot be measured by touch probes・Tool path vector compensation “VectPath”
Advanced machining error compensation technology
Without re-modeling and re-generation of tool path to compensate for machining errors
Reduce the number of tools used
High speed aerostatic bearing spindle
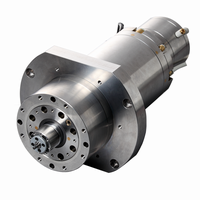
Spindle speed: 60000 min-1
NRRO(*): 0.10 μm
TIR: 1 μm
(*) Measured with the method of Single Point Asynchronous Error Motion
1. High speed and low heat generation
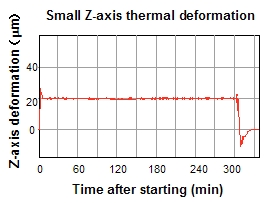
- Improvement of machining time
- Reducing in the types of tools and the processes (small diameter tool use)
- Low spindle thermal displacement (See the figure at right)
2. High rotational accuracy
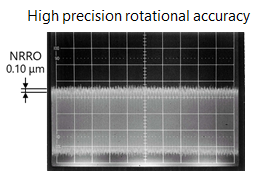
- Realization of high quality machined surface
- Enhanced tool life
3. Virtually unlimited life of bearings
- Availability of high speed, continuous machining
- Reduction in the maintenance cost
4. Low level vibration and noise
- Realization high quality machined surface
- Improvement of the working environment
Comparison of the spindle functions
Item | Ball/roller bearing spindle | Aerostatic bearing spindle |
---|---|---|
Bearing life | 2000∼3000 hour | Virtually unlimited |
Continuous running time | Within a few hours | Virtually unlimited |
Drive motor | Several 10 kW | 1.8 kW |
(Extremely consumed by generation of heat, noise, vibration) | ||
Tool life | Shorter (Due to the low rotational accuracy) | Longer (Due to the high rotational accuracy) |
Spindle exchanging time required and the cost |
2∼7 days Expensive | 2∼3 hours Cheaper |
Linear motor drive
High precision contouring
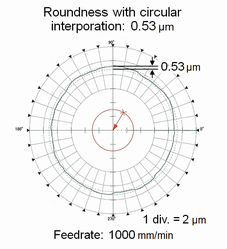
High quality surface machined with high speed feedrate is realized, providing linear motor driving system for X, Y and Z axis.
- High quality and smooth machining around quadrant switching area realized, due to minimized lost motion.
- High quality flat surface realized, due to eliminating factors, for instance, influenced by a ball screw driving system.
High precision positioning and smooth feed
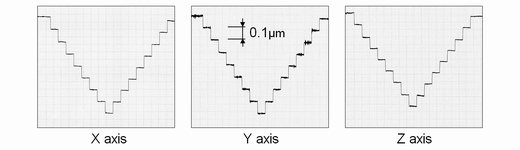
Reliable step feed 0.1 μm realized, providing 0.01 μm of programming resolution for X, Y and Z of linear 3 axes.
Efficient cooling system
UVM-450C(H), UVM-700C(H)
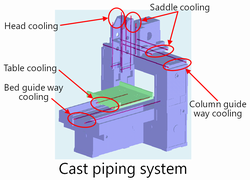
Improve thermal stability and minimize thermal distortion.
Casting pipes in the machine body is Shibaura Machine's own development.
UVM-450D(H), UVM-700E(5AD)
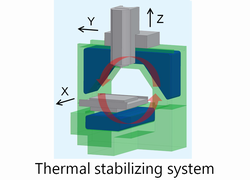
Thermal stabilizing system allows high-precision machining for long hours.
Circulates a temperature-controlled liquid through the structure.
Variety of applications
(1) Vertical rotary and indexing table (C1 axis)
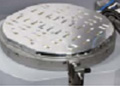
Examples
- Crossed groove machining
- Turning
- Fresnel lens machining
(2) Tool swiveling and indexing head (A axis)
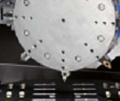
Example
- Groove machining
- Groove machining with gradually changing angle
- Automatic tool changing (turret)
Options for automation and unmanned operation
1. Automatic tool changer(ATC)
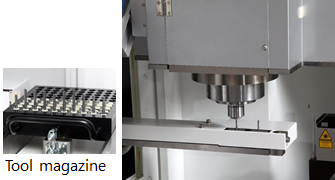
Automatic tool changer to support efficiently a long hour operation
(1) Tool direct chucking system
(2) Shank size of tools:
Either one of φ4mm and φ6mm
(3) Tool storage capacity: 50 tools(OP: 100 tools)
2. Automatic tool length measurement device
Compatible with optical Image sensor type, laser line sensor type, and laser beam sensor type
3. Automatic work piece measurement device
Measurement function according to the machining target (shape / dimensions, free-form surface, geometric shape dimensions)
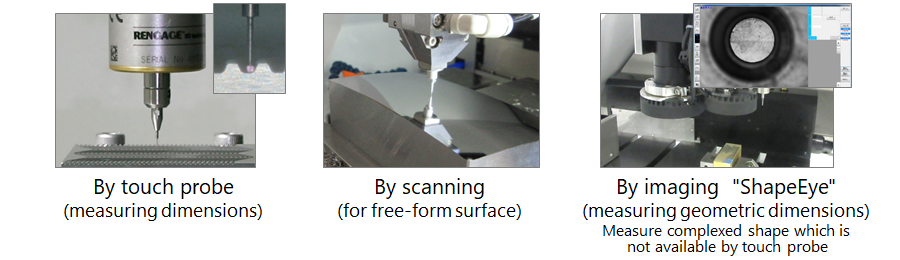
4. Total support application software “UVM-TSA”
"UVM-TSA" is the multifunctional software to contributes an improvement of customer’s productivity
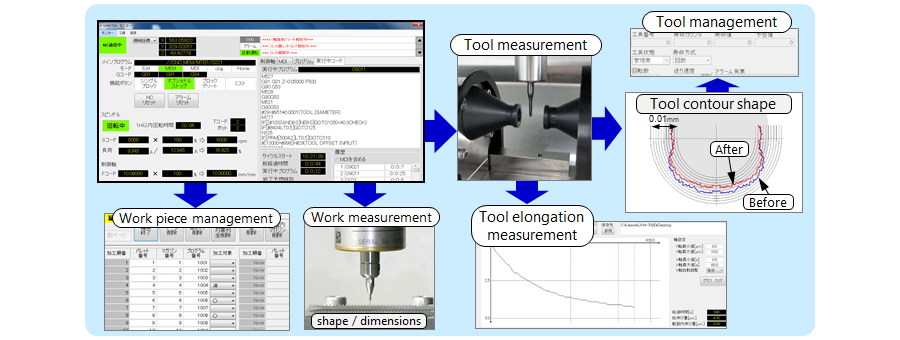
5. Tool path vector compensation “VectPath”
Advanced machining error compensation technology
To improve machining accuracy by avoiding a difference of cutter contour shape
Without re-modeling and re-generation of tool path
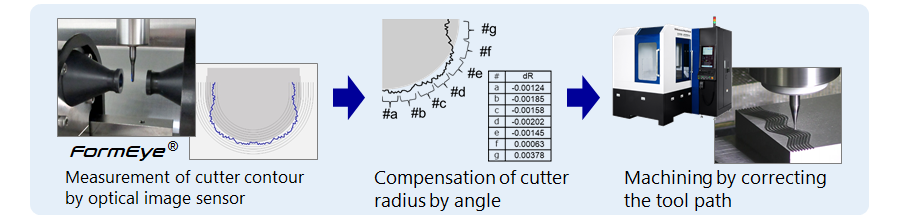