machiNet Example
Collect:TM Smart Sensor
Shibaura Machine's original IoT sensor system
Multi-sensor that can measure one machine vibration and temperature
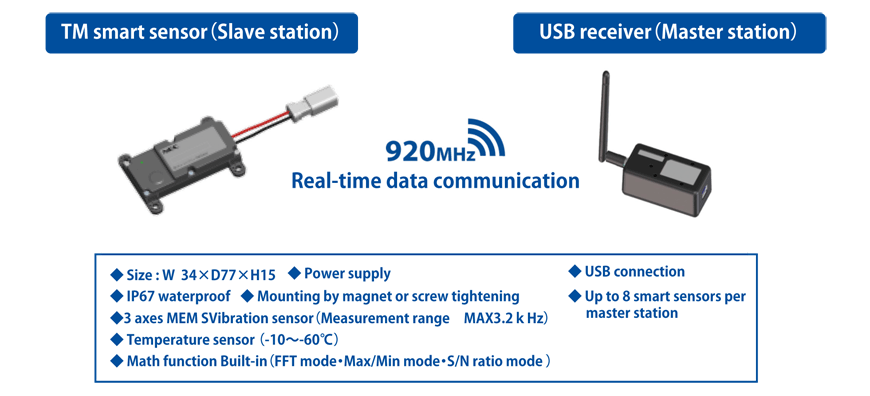
Shibaura Machine developed the TM Smart Sensor as a basic sensing device for machines. TM Smart Sensor is an IoT device that combines the acceleration sensor and temperature sensor for the X, Y, and Z axes into a single IoT device, and the collected data is sent to an edge computer over a wireless connection. Compared to a high-precision sensor, this acceleration sensor is cheaper and easier to install, allowing it to be used on any location on industrial machinery. The TM Smart Sensor was developed under a concept where multiple sensors are mounted on the machine for capturing changes in the machine status and finding anomalies as quickly as possible. Once any sign of an anomaly is detected by the TM Smart Sensor, the machine can be diagnosed using a high-precision measuring instrument, or a service technician can inspect the machine for problems.
Connect:Supports various open protocols
Synchronize with any machine or sensor using smart factory compatible protocols
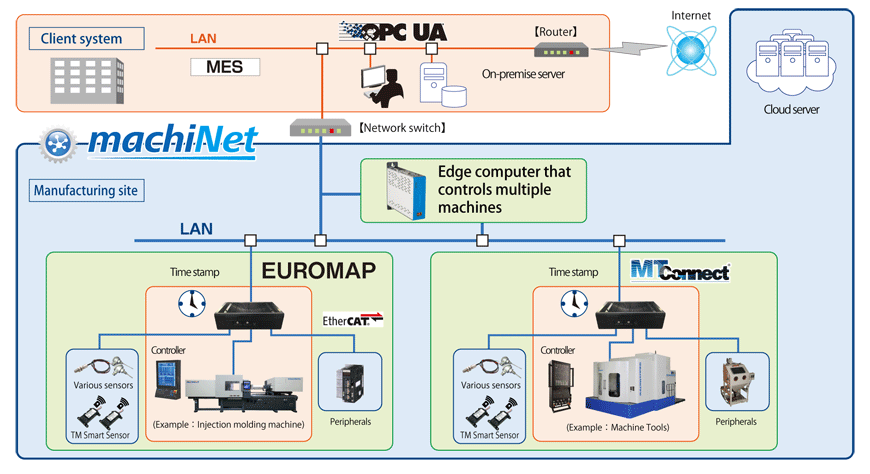
The focus of machiNet is factory manufacturing processes. Under this concept, areas such as MES (Manufacturing Execution System) and ERP (Enterprise Resource Planning) are handled under a different upper-level system. Government level policies for the digitalization of the manufacturing industry, such as Japan's Connected Industries initiative promoted by the Ministry of Economy, Trade and Industry and Europe's Industrie 4.0, are well-known, and use of the standard protocol known as OPC UA is typical in these architectures. For this reason, the machiNet platform is also provided with an interface that assumes use of OPC UA to connect to upper-level systems.
Visualize:ViSCAS-S
Vibration Sencer data collection and Analysis System-Simple edition
Display short-term vibration data in waveform, min / max, FFT
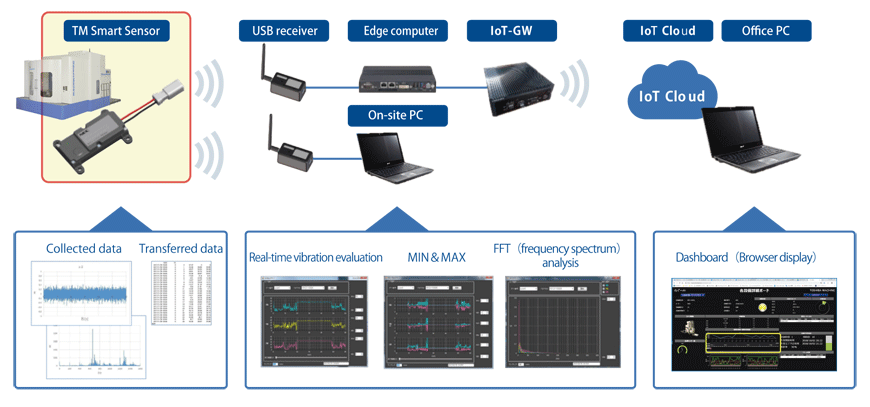
The machiNet platform includes the ViSCAS-S Vibration Sensor data Collection and Analysis System for enabling online analysis of the collected vibration data.
ViSCAS-S is linked with our CNC system and uses the vibration data collected when a preset operation pattern is applied to the machine for analyzing the state of deterioration and conducting predictive maintenance. To implement predictive maintenance, the vibrations are measured, and from this obtained data, AI (machine learning) is used to calculate the characteristic values and perform modeling for the normal state. Once modeling is completed, model data is compared to vibration data that was measured during day-to-day operations for automatically determining if anything is abnormal. The key feature of this method is that it can be easily started without any particular need to be aware of threshold values.
Analyze:Analysis of vibration sensor data
Analyze long-term accumulated vibration data using quality engineering technology
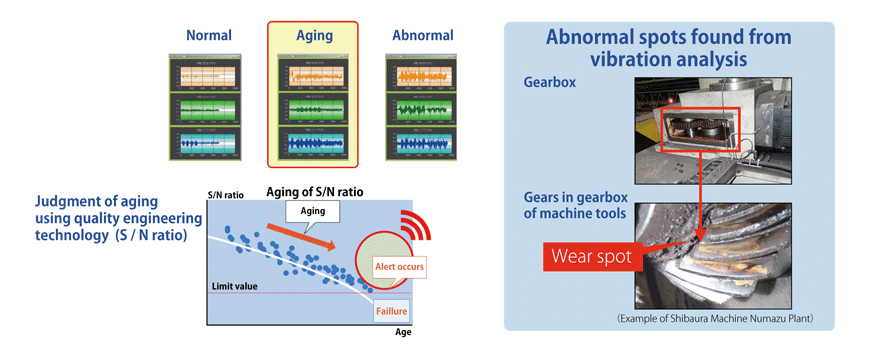
The TM Smart Sensor stores a certain volume of data within the sensor, where the FFT (frequency spectrum), maximum and minimum values, signal to noise ratio (S/N) (metrics for assessing the quality engineering technology and size of the dispersion), and other values are calculated, and the results are sent to an edge computer. Sensors are installed in the mechanical sections of machine tools and other equipment for continuously analyzing the S/N of vibration waveforms for replacing the analog information known as waveforms with digital data that enables visualization. This allows easy identification of changes from the normal state for more accurate predictive maintenance.