小口径レンズ専用のガラス素子成形装置を開発(小口径金型によるマルチチャンバ化と自動化を実現)
2001年7月6日
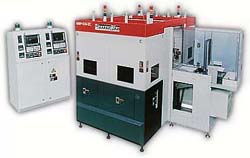
当社は、このほど小口径レンズ専用のガラス素子成形装置GMP-106-2C「写真:4チャンバタイプ」の開発に成功し、販売を開始しました。
光通信部品用小口径レンズの代表的な使用例として、LD(レーザーダイオード)モジュールがあります。同モジュールは、電気信号を光信号に変換する重要部品であり、LDから出たレーザー光を、光導波路のコア部分にいかに精度良く集光させるかがポイントです。そのため、同モジュール用集光レンズには、直径2mm以下の小口径非球面レンズの採用が進められてきていますが、従来までのレンズ製作法(研削加工)では、レンズが小口径であることによる研削難や、需要量への対応などに課題がありました。
当社は、小口径のガラス素材を加熱・軟化させ高精度に加工された金型を用いてモールド成形する、専用のガラス素子成形装置を新たに開発することにより、この課題を解決し、小口径レンズを高精度かつ大量に生産することに成功しました。
小口径ガラス素子成形装置GMP-106-2Cは、特殊な赤外線ランプを用いて金型温度の均一化を図ると共に、ACサーボモータとガラス素子成形装置専用に開発した自社製制御装置の組合せにより、正確な位置制御とトルクフィードバック方式による正確なプレス力制御を可能としました。従来のGMPシリーズの特長はそのままに、小口径金型(最大取付け金型径:φ65mm)のマルチチャンバ(2~4軸)方式の採用と、当社スカラロボット(SR-505HSP)を組み合せたシステム構成により、高精度のガラス成形に加え高い生産性と自動化を実現しました。その他の主な仕様は、最大加熱温度が800℃、最大プレス力が13KN(1,327kgf)となっています。
主な特長
- チャンバサイズの小型化により、高精度な小口径ガラス素子成形に特化。
- マルチチャンバ化(4チャンバ)により、高生産性を実現。
- 自給装置・ワークストッカの付属により、自動化・量産化に対応。
- 新型の赤外線ランプユニットにより、金型の均一加熱性を向上。
- 高精度プレス機構により精密成形が可能。
- 高速加熱、高速冷却方式のため高生産性を実現。
- 精密温度プロファイルが実現可能。
- 成形条件の再現性が優れ安定。
主な仕様
金型寸法 | 標準サイズ | 直径60×t40mm |
取付可能な外径 | 直径52~65mm | |
チャンバ数量 | 4(2チャンバ/1台×2台) | |
加熱温度 | 最大 | 800℃ |
常用 | 750℃ | |
プレス力 | 最大 | 13kN(1327kgf) |
常用制御範囲 | 0.2kN~10kN(20~1020kgf) | |
プレス軸ストローク(標準サイズ時) | 85㎜ | |
機械的精度TILT(ツギテ間、常温) | 傾き30″以内 |